NASA astronaut describes for students how 'test to failure' protected shuttle after Columbia loss
By Anne Ju
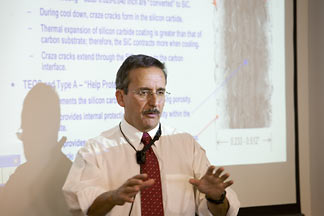
NASA astronaut and engineer Charles Camarda visited a Cornell engineering class Nov. 21 to recount his experiences onboard Discovery, the first space shuttle mission following the 2003 loss of Columbia and its seven crew members. He also discussed his role in the Columbia accident investigation.
Camarda described for the Collaborative Engineering Design class how teams conducted analyses and tests to improve understanding of what caused the accident and designed new safety measures for future missions.
The course, cross-listed between mechanical and civil engineering, is a collaborative effort with Syracuse University that is funded by NASA, and it requires students to design parts of a space vehicle. The partnership was established in 2001 and continues to be led by Alan Zehnder, professor of theoretical and applied mechanics.
STS-114, the July 2005 Discovery mission, was an experimental endeavor for designing and implementing new inspection and repair techniques for space vehicles. The crew also delivered much-needed supplies to the International Space Station.
Camarda, one of seven Discovery crew members, emphasized the importance of "collaborative engineering" in the period leading to the launch. For many months before the mission, the crew and other scientists worked together to scrutinize every aspect of the Columbia disaster and thought of new ways to protect against future occurrences.
One end result of their work Camarda described was the creation of several methods that would allow in-flight repairs to damaged tiles or the reinforced carbon-carbon (RCC) leading edges of the spacecraft.
Columbia, it is now known, met its demise as the result of a piece of foam separating from the external tank during launch, hitting the vehicle's leading edge -- the forward part of the wing. The foam pierced one of the leading-edge panels, made out of RCC, allowing ingress of hot gas during re-entry that rapidly burned through the wing structure and resulted in the total breakup of the vehicle about 37 miles above Dallas-Fort Worth.
Nothing in engineering design is clear-cut, Camarda said, and nowhere is that more true than in spacecraft design.
"You have an interplay between analysis and experiment," Camarda said. "You don't always have perfectly fixed boundary conditions. You explore what your experimental situation is, how well it models your model of the real world, and you go back and forth. You test to failure, in an attempt to understand the critical failure mechanisms. When you understand the limits of performance, then you have an accurate picture of what margin you actually have in your design."
The new repair techniques, which NASA spent more than $1 billion developing, were labored over by engineers who first had to establish the parameters by which an accident like Columbia could occur. NASA spent months collecting debris from Columbia over parts of Texas to reconstruct what happened.
"What we did not understand was that the foam, as light as it was, could cause critical damage," Camarda told the class.
Engineering graduate student John Emery said Camarda's insights into damage analysis were particularly enlightening. "It was interesting to hear that whenever you do mechanical tests, you should test the failure," he said.
Media Contact
Get Cornell news delivered right to your inbox.
Subscribe