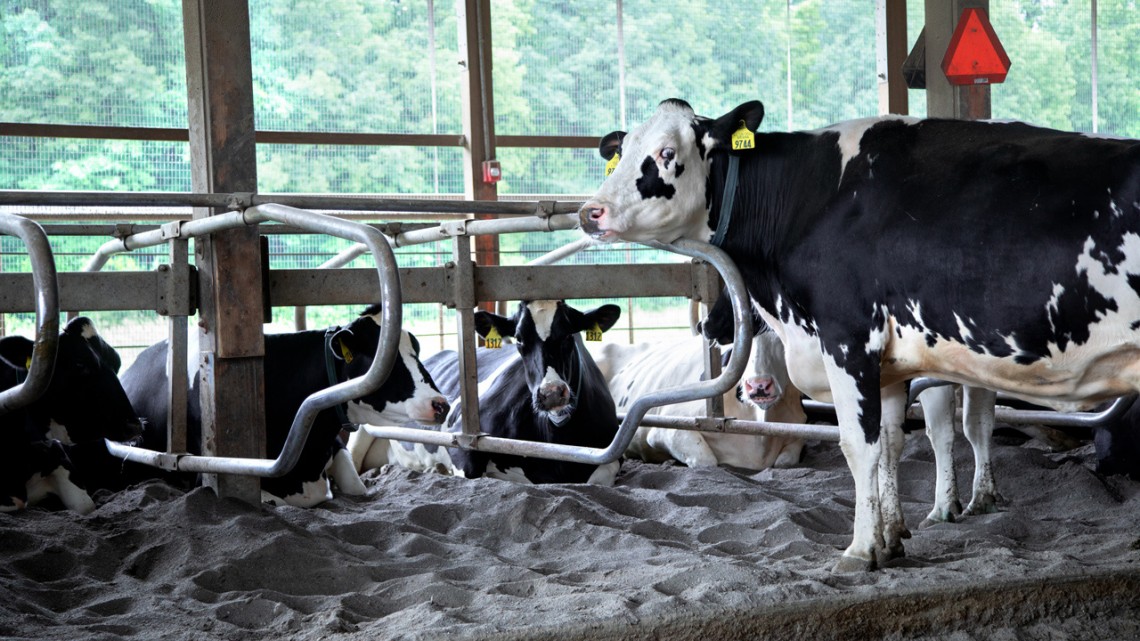
Cows relax in the sandy stalls of the College of Veterinary Medicine's Teaching Dairy Barn.
Dairy barn implements poop-to-power system
By Blaine Friedlander
Cornell’s College of Veterinary Medicine Teaching Dairy Barn – home to 200 cows – has installed a state-of-the-art system that separates manure from sand bedding material, providing clean bedding for the cows and creating muck perfect for making electricity and heat.
Dairies also use sawdust, wood chips or straw as bedding material, but sand reduces potential bacterial growth while maximizing cow comfort, said Paul Jennette, the veterinary college’s director of biocontainment operations.
“For manure management, we have to do something with all of this manure with sand in it,” said Jennette. “Pumping the sand-laden manure into a lagoon or holding tank or onto a truck is difficult, because the sand settles – not to mention the sand is abrasive on the pumps.”
Manure is conveyed into the new separator, adjacent to the barn. Minutes later, clean sand emerges ready for another day’s use; liquid manure is collected in a tank for removal.
The system recovers more than 95 percent of the sand for the teaching dairy to reuse. Instead of importing 30 tons of sand weekly, the dairy now only purchases new sand when needed.
Here’s how it works: A pump draws sand-laden manure out of the reception pit; it is diluted with recycled water and filtered through a screen that removes bits of hay and other debris. A high-speed pump then pushes the diluted sand and manure through a cyclone that separates most of the manure from the sand. The sand with some residual manure flows into a sand washer where an auger brings up the sand, which is then sprayed with tap water as a final cleaning step.
Captured liquid manure is trucked to the Ithaca Area Wastewater Treatment Facility, where microbial activity breaks down the manure – along with other organic matter – generating methane gas in the facility’s anaerobic digester, said C.J. Kilgore, chief operator of the facility.
The digester’s methane gas is then used to run microturbines to generate electricity. In turn, the turbines create heat, which is also captured. “Literally, the manure helps us to run the anaerobic digester and provide power for our facility,” Kilgore said. “We’re creating electricity and extra heat while we’re reducing our electric load.”
In 2012, the veterinary college’s barn gained national acclaim for its design and was LEED (Leadership in Energy and Environmental Design) certified by the U.S. Green Building Council for its energy efficiency.
Said Jennette: “The new separator makes us more self-reliant and we’re making our dairy operations much more sustainable.”
Media Contact
Get Cornell news delivered right to your inbox.
Subscribe