Simple twist becomes twist of fate, as new technique could revolutionize electronics with pure, defect-free single crystal films of any kind on a substrate
By Larry Bernard
Cornell University scientists have achieved a "Holy Grail" of materials science -- pure, single crystal growth of any film on a semiconductor substrate, a technique that holds promise to revolutionize electronics.
"This is preliminary work, but if it truly works -- and we think it will -- it definitely could revolutionize the microelectronics industry," said Yu-Hwa Lo, Cornell associate professor of electrical engineering who led the work. "This is a whole new way of doing things. The potential is very great, unimaginable really, but we don't know yet if it will actually happen. We have demonstrated that it is possible."
Lo and his doctoral student, Felix E. Ejeckam, and colleagues have for the first time demonstrated a "universal substrate" on which a crystal of any material can be grown. The technique opens the door for manufacturing whole new classes of devices in optoelectronics and microelectronics, for such items as new lasers, detectors, sensors, imaging systems, signal processing and computer chips, compact discs, data storage and dozens of other examples. The ability to grow single crystals of any material on silicon, for example, may breed an entire new generation of electronics.
Their research paper, "Lattice engineered compliant substrate for defect-free heteroepitaxial growth," is scheduled to appear in Applied Physics Letters (March 31, 1997, vol. 70, 10), by Lo, Ejeckam, Shanthi Subramanian, former Cornell doctoral student in materials science and engineering now at Exxon Research and Engineering Co.; and Hong Q. Hou and B.E. Hammons of Sandia National Laboratories.
The Cornell team also presented their work at the Institute of Electrical and Electronics Engineers Lasers and Electro-Optics Society annual meeting in November 1996 in Boston, by Lo, Ejeckam and Matthew Seaford, Cornell doctoral student also affiliated with the Air Force Wright Patterson Laboratory where he did this research, and the Sandia researchers. And it will be presented in May at the International Conference on Indium Phosphide and Related Materials in Hyannis, Mass., and the Materials Research Society meeting in San Francisco on March 31.
The research was funded by the Office of Naval Research; the Defense Advanced Research Projects Agency; the Materials Science Center at Cornell, which is funded by the National Science Foundation (NSF); and the Cornell Nanofabrication Facility, which also is NSF-funded.
Semiconductors are tiny crystals, such as silicon or germanium, that conduct electricity. They are the heart of all integrated circuits, which power everything from computers to cellular telephones to fiber communication networks. A major obstacle to the manufacture of various semiconductors is that the single-crystal semiconductor thin films must be deposited on a crystal of the same structure. For example, a light-emitting gallium arsenide thin film must be deposited on a gallium arsenide bulk substrate, or else defects will result and the semiconductor cannot be used.
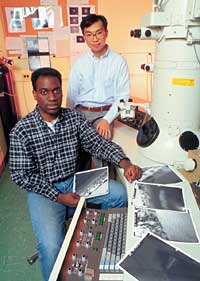
Each single crystal is characterized by its lattice structure and lattice constant. When a crystal layer is grown on a bulk crystal substrate, even a mismatch of 1 percent in their lattice constants causes problems. But the Cornell technique, for which Cornell has applied for a patent, shows that a mismatch of 15 percent can be overcome -- a feat previously unachievable.
The Cornell team solved that problem by what might be called a simple twist of fate. By rotating a thin film slightly and bonding it to a substrate, the surface of this new substrate becomes flexible, or compliant, and a crystal of any material can grow on its surface. They call it a twist boundary, in which the crystal materials are bonded by angular misalignment; and they call the new substrate, a new compliant substrate.
"It's ingenious," said Stephen Sass, Cornell professor of materials science and engineering, who was the Ph.D. thesis adviser for Subramanian and has been following the work through discussions with her, Ejeckam and Lo. "I've studied twist boundaries for years and I still don't understand how the boundary/thin film substrate combination is able to accommodate such large mismatches in atomic plane spacing. The results are striking, almost too good to be true. It's a very exciting discovery and I'm eager to look into the science underlying it."
The Cornell team demonstrated the technique with thick, pure crystal layers of indium gallium phosphide, gallium antimonide and indium antimonide, with mismatches as high as 15 percent. They successfully grew these crystals on a gallium arsenide wafer that had a flexible layer thin film. With traditional methods, it would not have been possible.
The Cornell team, in collaboration with researchers from the Wright Patterson Laboratory and the Sandia Laboratory, has demonstrated that the defect density in an indium antimonide layer has been reduced by at least 100,000 times with the new method, compared to the conventional method. This means that indium antimonide crystals can be grown on gallium arsenide, to form the basis for infrared detection and a Hall sensor -- a sensor that has been used in airplanes and soon will be used in automobiles.
If this can be done for another compound semiconductor, gallium nitride, which has a lattice mismatch of about 20 percent, then high-quality blue and ultraviolet lasers as well as high-temperature, high-power electronic circuits can be fabricated. Blue lasers, rather than red, will be used in the next generation of compact discs, for example, because the shorter wavelength stores more data. High-powered electronic circuits that can also withstand high temperatures are used in automobile, aerospace, communication and power industries. The Cornell team expects it can be done with this technique, and they are in the process of trying it.
The researchers also believe that the crystals can be grown on silicon wafers, opening the door for computers that, for example, could have different types of semiconductors operating at the same time on the same motherboard.
In microelectronics, the next generation ULSI (Ultra Large Scale Integrated) circuits can be made using this technique. If the technique is successful on a silicon substrate, then no other substrate material would be needed, the researchers say. Since this lattice engineering technique is a structural phenomenon, there is no reason why it should not work with silicon.
"This new concept and technique enables the growth of numerous high-quality, new compound semiconductors that cannot otherwise be achieved due to lack of adequate substrates," the authors write. "With further research, this work will lead to the production of 'universal substrates' on which compound semiconductors of nearly any lattice constant and crystal structure can be grown without defects."
"This is a nagging problem in the semiconductor industry," said Ejeckam, who expects to receive his Cornell Ph.D. in June and who contributed to the work as part of his doctoral thesis. "You can't grow gallium arsenide crystals on silicon. People are always trying different techniques, but they all had a major problem. We were looking for something universal that would be far-reaching with wide impact. It also had to be easy to implement. And we found it."
Ejeckam was pleased to be part of the research team. "It's rare that one gets to be present at the embryonic stages of a new field," he said. "We are going to be able to make whole new devices in optoelectronics and microelectronics. This is the seed for a whole new area, and it has an extremely high potential to change the field. Whether it truly can be sustained over decades, we can't tell. But the applications are wide-ranging and they span so many areas in materials science and electrical engineering. It's universal."
He added: "No one has ever seen anything like this before. And this is just the outer layer of the onion."
Media Contact
Get Cornell news delivered right to your inbox.
Subscribe