Energy harvester rolls to market production
By Blaine Friedlander
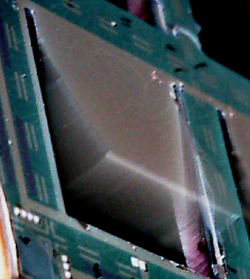
Farewell, expensive single-charge batteries. A new concept becomes proven reality, as MicroGen’s nanotechnology-based energy harvester – researched and developed by the company at the Cornell NanoScale Science and Technology Facility (CNF) – begins commercial-scale production this summer.
Batteries – like AA or AAA or lithium batteries – are often cost prohibitive for industrial or commercial entities using wireless sensors in distributed “smart” networks. “Sensors observe equipment status and condition, process automation control points, energy usage and many, many other critical parameters,” says Robert Andosca, president and CEO of MicroGen Systems Inc. of Ithaca, N.Y., and Rochester, N.Y.
“There’s not only the cost of the batteries, but there is labor cost in continually replacing them. With these energy-harvesting devices, it will save prohibitive battery replacement and associated labor costs,” says Andosca.
MicroGen’s BOLT micro-power modules (MPM, a complete battery replacement unit), destined for the U.S., European and other markets, gather ambient vibration much like a windmill grabs the breeze and changes it into energy.
In industry parlance, this is a “piezo-MEMS” – or, piezoelectric microelectromechanical systems – device. The low-cost piezo-MEMS energy harvester chips are currently fabricated at the X-Fab MEMS Foundry in Itzehoe, Germany.
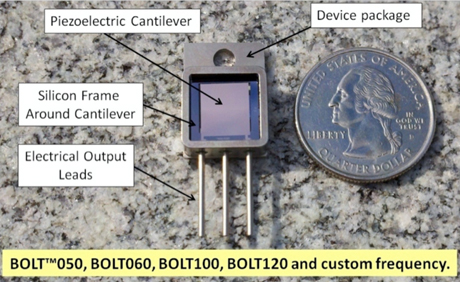
MicroGen’s energy harvester had humble beginnings at the National Science Foundation-funded CNF, as MicroGen and CNF staff developed prototypes. “If we are to realize the economic impact of nanotechnology, it is vitally important that the prototyping activities in the lab get translated into products that form commercial ventures,” says Don Tennant, director of operations at CNF.
Andosca concurs. “The CNF and its staff were key to MicroGen’s development, which has allowed us to get our green, battery-free micropower sources to market,” he said.
The micropower generator is a low-cost, long-lifetime device that scavenges otherwise wasted vibrational energy. Vibration causes the tiny micro flap in the device to swing back and forth, which generates electrical current that charges an adjacent ultra-capacitor or rechargeable thin-film battery. In an automobile’s tire pressure sensor, for example, this device collects the vibrations from the tires meeting the road and offers unending power for the sensor.
The convenience: a car’s owner never has to worry about replacing sensor batteries in awkward places. The environmental impact: eliminating 164 million depleted coin-cell batteries each year that would otherwise need to be recycled.
Uses for these energy devices could include industrial, building and commercial wireless sensor markets, machinery monitoring, lighting control and smart utility metering. They could also be used in transportation systems, civil infrastructure monitoring and asset tracking. They could help report outside temperatures at vineyards and help power wireless price tags at stores.
About three years ago, MicroGen obtained a portion of its startup funding from Cornell’s Energy Materials Center and the New York State Energy Research and Development Authority (NYSERDA) to support research on this product at the CNF. Eventually, the company will reimburse NYSERDA through royalties, now that commercial scale production will soon begin. The funding enabled MicroGen to build, test and redesign the product to ensure that the energy harvester met industry standards for wireless sensor unit power levels.
Says CNF’s Tennant: “MicroGen is a great example of how we can work with companies in order to turn their ideas into designs that are practical to mass produce at commercial fab facilities.”
Media Contact
Get Cornell news delivered right to your inbox.
Subscribe