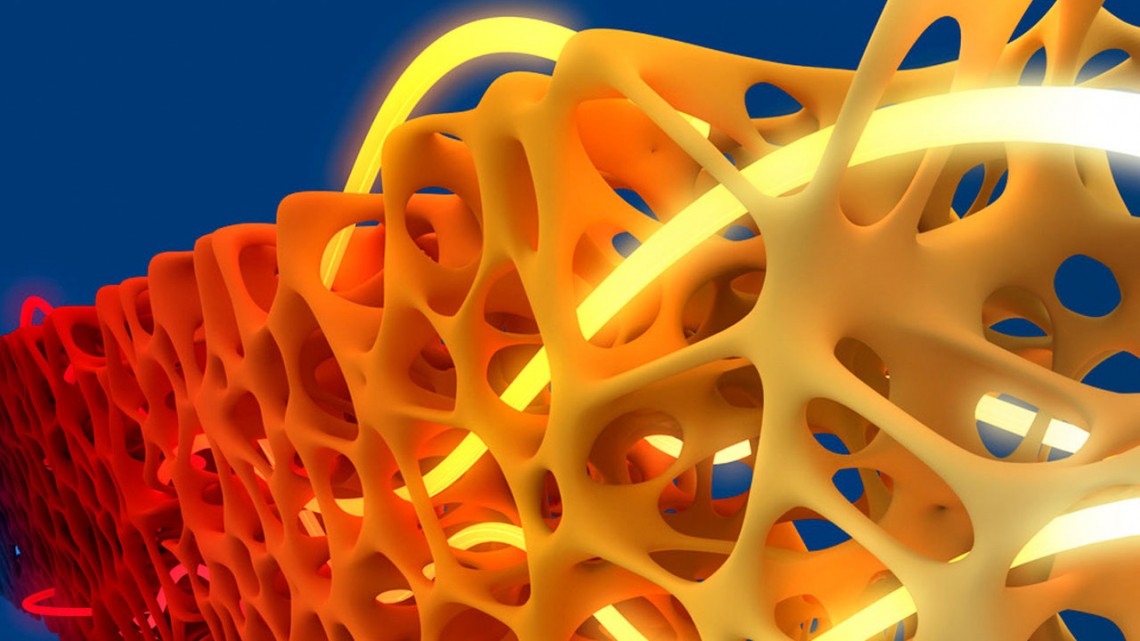
An artist’s rendering of fluid strategically guided through a ceramic structure’s pores. Using a manufacturing technique researched by Cornell’s Sadaf Sobhani, tailored porous structures hold new opportunities for applications in thermofluidic systems.
Technique could enable better custom ceramic fabrication
By Syl Kacapyr
Ceramic structures filled with tiny macroscopic pores play an important role in industrial and biomedical products, but they’re also notoriously difficult to fabricate.
A Cornell researcher may have an answer, as a manufacturing technique she’s developing has introduced a new level of precision to porous ceramic materials, opening a new realm of possibilities for their application.
The technique – created by Sadaf Sobhani, assistant professor of mechanical and aerospace engineering – uses a combination of computational modeling, porous structure design and 3D printing to precisely customize the porous network. The technique is published in the paper “Additive Manufacturing of Tailored Macroporous Ceramic Structures for High-Temperature Applications,” featured in the August issue of Advanced Engineering Materials.
Porous ceramics are used in bioreactors, insulators, automobile engines and synthetic bones because of their mechanical strength as well as their ability to resist heat and corrosion, among other properties. By manipulating the geometries within the ceramic’s complex network of pores, engineers can achieve different properties. But most manufacturing techniques, such as molding and foam processing, make it difficult to tailor those geometries.
Digital light processing lithography is a type of 3D printing that, unlike other ceramic 3D-printing techniques that deposit material across a build platform, projects light patterns onto layers of a photocurable resin. The resin then solidifies where it has been exposed to light, retaining the pattern projected onto each layer.
Sobhani uses lithography with a ceramic-loaded resin. Once the resin has been treated by blue light, the ceramic particles remain suspended where the resin has solidified. The printed object is then placed into a series of furnaces that burn off the resin and cure the remaining ceramic.
“The technique enables you to make things that you just couldn’t make with a mold or other traditional ceramic manufacturing methods,” said Sobhani.
As a proof of concept, Sobhani fabricated two samples of alumina porous ceramics, with different pore geometries. She and her colleagues then studied the samples in a combustion experiment and assessed the flame stability inside the porous structure. The samples, both made from the same resin-ceramic mix, produced dramatically different results due to their distinct porous structure designs.
The ability to fabricate customized ceramics with such precision can inform what the materials are used for, but it also means the printing technology must be perfected.
“If your printer or thermal-treatment methods are a bit off and cause deviations from your very precise geometry, the final product is going to have a different performance than what it was designed for,” Sobhani said. “So part of my next research will focus on geometric accuracy and using X-ray diagnostics to quantify those errors and alleviate them.”
Sobhani’s future research will also focus on identifying new applications that can take full advantage of the fabrication technology. She has acquired a high-density ceramic lithography printer for her lab – the first on campus – and said she is looking forward to collaborating with researchers who have innovative ideas for everything from energy and thermal-management systems to biomedical applications.
“Previously, if you wanted to build this really complicated porous matrix that’s graded in a certain direction, but not the other, or has some functionality in thermal conductivity, those would have always just remained as ideas,” she said. “But now with 3D printing, there’s a new realm of possibilities and the question has become, ‘What should we make?’”
The study’s collaborators include Matthias Ihme, professor of mechanical engineering at Stanford University, and manufacturing company Lithoz America. The research was supported by NASA and the National Science Foundation.
Syl Kacapyr is public relations and content manager for the College of Engineering.
Media Contact
Get Cornell news delivered right to your inbox.
Subscribe