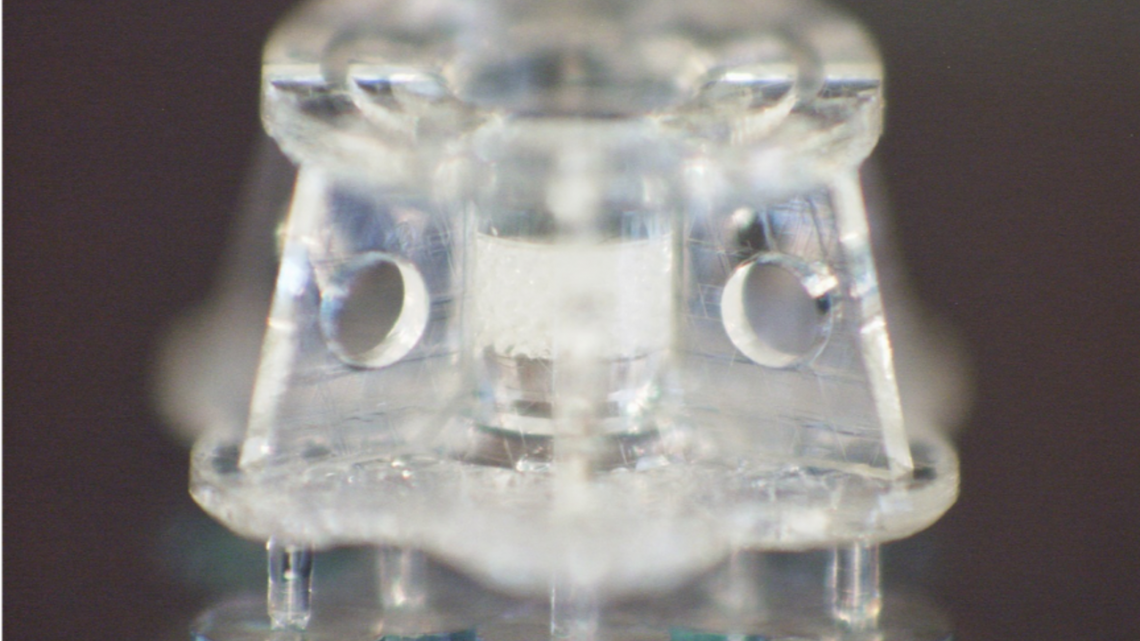
3D-printed gas diffusion layer for an electrochemical reactor, printed at the Cornell NanoScale Science and Technology Facility using two-photon polymerization.
Study highlights promise of 3D printing for electrochemical reactors
By Syl Kacapyr
Electrochemical reactors that can capture carbon dioxide and transform it into valuable products are a relatively new and promising technology for reducing greenhouse gas emissions. While many challenges exist to scaling up the technology, a new study highlights the benefits of using 3D printing, also known as additive manufacturing, to significantly improve cost, yield and efficiency.
In electrochemical reactors like those that were studied, gaseous carbon dioxide travels through a porous gas diffusion layer for distribution to the catalyst, where it dissolves into a liquid electrolyte and converts to various products like fuels, lubricants and polymers. Using additive manufacturing to rapidly prototype reactors with unique shapes and topologies, designs could be optimized for improved conversion rates, according to study co-author Sadaf Sobhani, assistant professor in Cornell University’s Sibley School of Mechanical and Aerospace Engineering.
“Instead of focusing on engineering the catalyst, electrode or electrolyte, we focused on how the geometry – the distance between the electrodes or connections between compartments – influences system performance,” said Sobhani, who began the research as a postdoctoral associate at the Lawrence Livermore National Laboratory before continuing the work at Cornell.
The findings are detailed in the study “Advanced manufacturing for electrosynthesis of fuels and chemicals from CO2,” published in the journal Energy & Environmental Science.
Computationally simulating the chemical phenomena inside reactors, Sobhani was able to identify the conditions leading to mass-transport limitation, where the rate at which carbon dioxide travels to the catalyst is slower than the catalyst chemical conversion rate.
“This can provide the framework for distinguishing the operational limitations for any reactor and system design,” Sobhani said, “as well as understanding the primary drivers that can lead to better designs to overcome these limitations.”
Sobhani is continuing her research into how geometry and surface properties influence overall reactor performance, leveraging the resources at the Cornell NanoScale Science and Technology Facility to print sub-micrometer surface features and advanced microstructures, and the Cornell High Energy Synchrotron Source, among other facilities, to image those features and study the internal operations of reactors.
“Electrochemical conversion reactors are inherently interdisciplinary systems, and I have found that working collaboratively is one of the key strengths of Cornell researchers,” Sobhani said. “My aim is to combine recent innovations in micro-advanced manufacturing, surface coatings and X-ray imaging to bring precision and control to gas-diffusion-layer design.”
Media Contact
Get Cornell news delivered right to your inbox.
Subscribe